How We Work
It is our goal to provide a clear understanding of what we at Total Tool Solutions need to provide you and your customers with the most comprehensive proposals and ergonomic systems possible. We have compiled a presentation that consist of six parts, an overview, material handling terminology, a description of the components of an ergonomic system, product descriptions and where they are best applied. This also includes an application data sheet, as well as system layout templates.
As we progress through this presentation your input with any questions or suggestions on how we may better serve you and your customers are greatly appreciated. The information gathering phase of any project is the most crucial part of ensuring success, as with anything “Quality In, Quality Out”.
We greatly appreciate the opportunity to work with you in meeting the ergonomic and material handling needs of your customers. Our goal is to work as partners to maintain open lines of communication to ensure a smooth flow of information. These goals are the keys to expanding both of our company’s opportunities with the existing and sure to be new customer base.
Anatomy of an Ergonomic System
In nearly all ergonomic systems, whether a tool or material handling application the solution will be made up of four parts. The lift, the suspension, the tool (end effector), and the controls, all of these components will vary widely from application to application. The lifts are available in many forms and configurations; the most common used are:
- Arms (Articulating & Manipulating)
- Cable Balancers (Pneumatic & Spring)
- Vertical Balancers (Also called Torque Tubes)
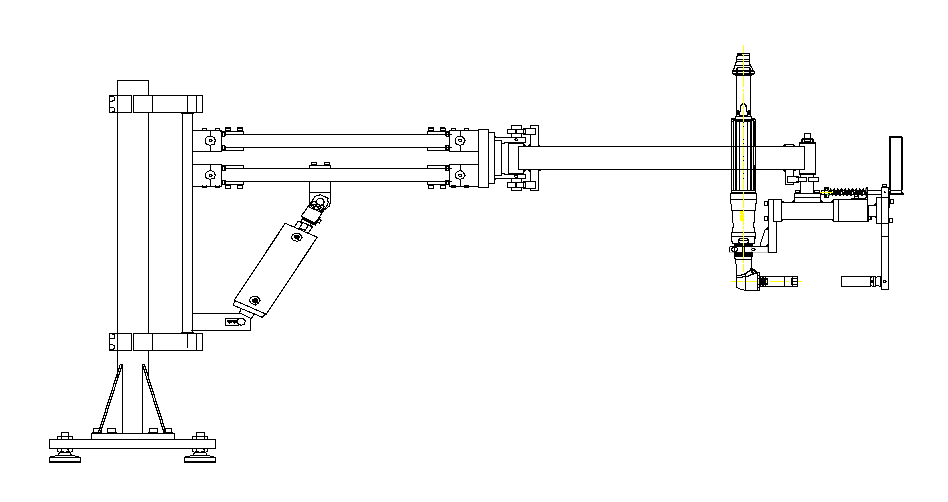
The suspension can consist of an overhead bridge and rail system; the bridge can be either single or dual girder. The runways in most instances will be a dual rail set up with or
without a bridge, however there are instances that a single
runway would be used such a tool rail or material handling application where the pick and place are in line. Other suspension options include floor, bench top, column or ceiling mounting.
The tool or also referred to as an end-effector can be as simple as a j-hook type for material handling or single compliant pinch clamp type for torque tool holding. This can also be the most complicated part of an application, using clamping, vacuum, and magnets. The end-effector provide tilting, rotation and manipulation of tools and materials. These attributes of an end-effector are the key to reducing the fatigue and injuries to operators that are associated with most assembly or material handling applications. In many applications the end effector will be specifically designed to fit the application at hand.
The controls range from the tensioning of a spring on a spring balancer, or single balancer regulator used in many nut-runner applications. Or can be as complicated as multiple load balances, and incorporate tilts, rotates and can be sequenced. These systems can either be pneumatic or PLC controlled, they can also interface with the controllers used with most DC nut-runner applications. This portion of a system like the end-effector in many applications will be designed specifically to fit a dedicated application.
Ergonomic Material Handling Terminology
A Mechanical means of attaching the cable of the balancer to the handling fixture. See “C” Bail.